5. JAPONSKI PROIZVODNI MODEL
Japonska proizvodna filozofija
Imre Cikajlo and Franc Gider
»Če on dela zate, delaš tudi ti zanj.« Japonski pregovor
Japonsko proizvodno filozofijo je pojasnil japonski inženir Šigeo Šingo (1909–1990). Njegovo delo [23] obsega prikaz proizvodnih procesov v proizvodnih obratih, znanih po zasnovi »poka yoke« (pri čemer statistično preverjanje kakovosti zamenja odkrivanje vzroka vsake napake, kar vpliva na spremembo proizvodnega procesa, da se napake odpravijo).
Filozofija je postala aktualna okrog leta 1970, v času največje naftne krize, ki je zahtevala korenite spremembe:
- proizvodnjo brez izvržka,
- proizvodnjo brez napak,
- točno časovno oskrbovanje (ang. Just in Time),
- brezizgubno poslovanje.
Proizvodni modeli stalnih izboljšav temeljijo na nenehnem iskanju potratnih aktivnosti (»smrtnih izgub«), ki jih lahko odpravimo z različnimi tehnikami in metodami. Identificiramo 7 najpogostejših različic težav, ki izhajajo iz znanih potratnih aktivnosti (Slika 120), in nekatere tudi uspešno zmanjšamo z uporabo sistemskih orodij (Slika 121).
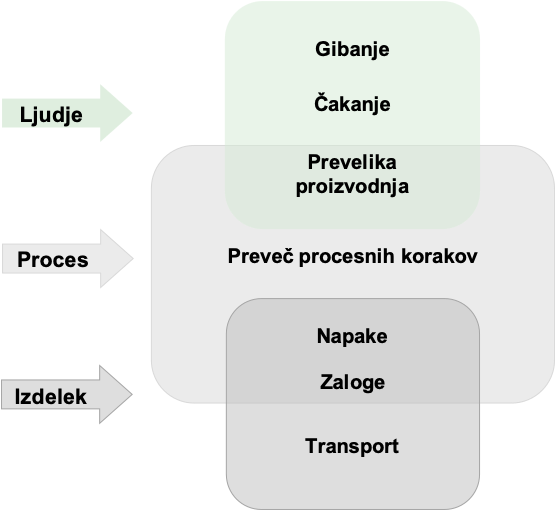
V japonski proizvodni filozofiji sta najbolj uveljavljeni metodi za uvajanje in vrednotenje stalnih izboljšav:
Z njima lahko dosežemo učinkovito uravnavanje in izboljšanje pretočnih časov, produktivnosti, medfaznih zalog, kakovosti in površine (Slika 121).
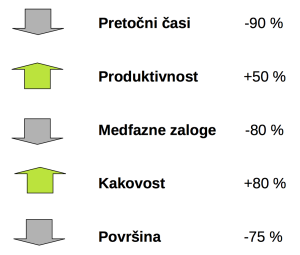
Kaizen
Kaizen (jap. kai – sprememba, zen – dobro) je japonska filozofija, namen katere je stalno izboljševanje procesov. Izhaja iz japonske zasnove timskega dela in prepričanja, da je vsak minimalni prispevek v pozitivni smeri pomemben za skupno izboljšanje stanja. Japonska družba je bila vso zgodovino usmerjena v timsko delo in skupne cilje oz. je delovala v skladu z miselnostjo »vsi delamo v dobro države in cesarja, ta pa nas varuje, nam daje zavetje ter možnosti za preživetje in zaslužek«. Še dandanes obstaja usmerjanje k timskemu delu v srednji šoli, in cilj te miselnosti ni individualen in sebičen razvoj posameznika, temveč družbe kot celote. Vsak posameznik mora svoje sposobnosti in znanje uporabiti tako, da koristi družbi.
Ena najuspešnejših filozofij 20. stoletja, ki je pripeljala Japonsko od obubožane države po 2. svetovni vojni do gospodarske velesile, je postala vodilo večine najboljših podjetij na svetu. Glavni elementi, ki so pripomogli k uspehu filozofije kaizen, so:
- kakovost,
- trud,
- vključenost vseh zaposlenih,
- težnja k spremembam,
- komunikacija.
Za dolgoročen in stalen uspeh podjetja so pomembni dejavniki:
- hitrost in prilagodljivost, ne stroški in produktivnost,
- univerzalna usposobljenost zaposlenih,
- neformalno komuniciranje zaposlenih v horizontalni smeri,
- univerzalni obdelovalni sistemi, ki se dajo programirati,
- organiziranje v time.
Japonska filozofija razlikuje tudi med stalnim, a počasnim izboljševanjem procesov, kar vodi do postopnega uveljavljanja blagovne znamke, kakovosti izdelkov, storitev, pridobivanja stalnih kupcev in inovacij (Slika 122), ki revolucionarno spreminjajo podobo, vendar imajo pogosto tudi zelo veliko dodano vrednost.
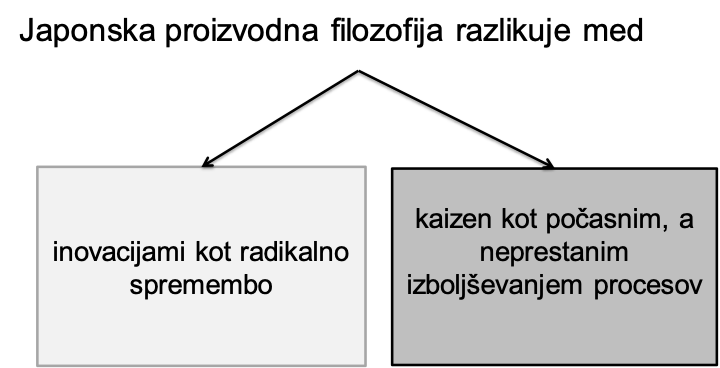
Orodja, ki jih uporabljamo v okvirih metode kaizen – postopno in neprestano izboljševanje procesov:
20 ključev
Metodo 20 ključev je razvil Ivao Kobajaši [22] in jo leta 1994 objavil pod imenom PPORF (ang. Practical Programme of Revolution in Factories). Po svetu se je za metodo, ki uporablja 20 postavk za ocenjevanje podjetij, uveljavilo ime »20 ključev«.

Glavni ključi so:
- KLJUČ 1 – čiščenje in organiziranje,
- KLJUČ 2 – organizacija sistema in ciljno vodenje,
- KLJUČ 3 – dejavnosti v delovnih skupinah,
- KLJUČ 20 – obvladovanje vodilnih tehnologij.
Dobro delujoč sistem temelji na teh ključih, ki so medsebojno odvisni in povezani – sprememba enega ključa lahko povzroči spremembo tudi pri drugem (Slika 123).
Ravnotežje in uspeh pri vseh 20 ključih vodita do poslovne odličnosti svetovnega formata.
Pet kategorij delovanja metode 20 ključev
Metoda pokriva 5 glavnih kategorij (motivacija M, kvaliteta Q, stroški C, dostava D in tehnologija T), v katere je razdeljenih 20 področij delovanja orodja (Slika 124). Doseganje višje ravni v področjih delovanja vodi do izboljšanja procesov v duhu »hitreje, bolje in ceneje« (Slika 123):
Cilji | 20 ključev | ||
Motivacija |
Dinamično delovno mesto | 1 | Čiščenje in organiziranje |
(Motivation) | 2 | Organizacija sistema, vodenje s cilji | |
3 | Aktivnosti delovnih skupin | ||
10 | Organizacija delovnega časa | ||
Kvaliteta |
Izboljšanje kakovosti | 7 | Proizvodnja brez nadzora |
(Quality) | 9 | Vzdrževanje strojev in opreme | |
11 | Sistem zagotavljanja kakovosti | ||
12 | Odnosi z dobavitelji | ||
15 | Širjenje usposobljenosti zaposlenih | ||
Stroški |
Znižanje stroškov (povečanje produktivnosti) | 13 | Odpravljanje vseh izgub |
(Costs) | 14 | Spodbujanje zaposlenih k izboljšavam | |
6 | Vrednostna analiza delovnih postopkov | ||
17 | Nadzor učinkovitosti | ||
19 | Varčevanje z energijo in materiali | ||
Dostava |
Izboljšanje toka, zmanjšanje medfaznih zalog, hitra dostava | 5 | Hitre nastavitve |
(Delivery) | 4 | Zmanjšanje medfaznih zalog | |
16 | Planiranje proizvodnje | ||
8 | Povezovanje proizvodnih procesov | ||
Tehnologija |
Razvoj tehnologije | 18 | Računalniška podpora poslovanju |
(Technology) | 20 | Obvladovanje vodilnih tehnologij |
Slika 124. Področja delovanja 20 ključev so razdeljena v 5 kategorij: motivacija (Motivation), kvaliteta (Quality), stroški (Cost), dostava (Delivery) in tehnologija (Technology).
Ocenjevanje
Vsak ključ ima petnivojski sistem ocenjevanja, ki je mednarodno usklajen in enak za vsa podjetja neglede na panogo, v kateri podjetje deluje:
- 1. stopnja – najnižji nivo – popolnoma neurejene razmere,
- 5. stopnja – najvišji nivo – odličnost svetovnega formata.
Skupna ocena podjetja se giblje med 20 (pri vseh ključih na 1. stopnji) in 100 (pri vseh ključih na 5. stopnji).
Ker ocenjevanje poteka po posameznih ključih, je pomembno vzpostaviti tak sistem ocenjevanja, v katerem upoštevamo frekvenco ocenjevanja, oddelek ali celotno organizacijo, skrbno izbiramo pri posredovanju informacij, vrednotenju rezultatov itn. Uvajanje sistema 20 ključev pogosto traja več let (> 5 let), v prvem letu gre za priprave, izobraževanje in razumevanje metode, v 2. letu za uvajanje metod in razumevanje povezave med njimi, v 3. letu že pričakujemo rezultate s postopnimi izboljšavami, v 4. letu postopoma zapisujemo postopke in standardiziramo postopke v podjetju, morda že dosegamo boljšo produktivnost, v 5. letu (in nadaljevanju) pa že pričakujemo vidne izboljšave, rast produktivnosti in prihodkov in izboljšanje klime v podjetju. Ko uspemo doseči 65 točk, lahko smatramo, da je podjetje napredovalo do minimalnih standardov odličnosti po merilih 20 ključev, za kar bi mu podelili bronasto medaljo. S 75 točkami si podjetje prisluži srebrno medaljo, kar pa metoda smatra že na nadpovprečno organizirano podjetje. Več kot 85 točk oz zlato medaljo po sistemu 20 ključev si je po merilih prof. Kobajašija prislužilo le 1 japonsko podjetje.
KLJUČ 1 – čiščenje in organiziranje
- Čisto in organizirano delovno mesto.
- Cilj sta čistoča in red, ki omogočata učinkovito in organizirano delo.
- 5. stopnja: vzroki nečistoče in nereda so odstranjeni. Delovni prostori so urejeni, zaposleni tudi sami vzdržujejo red in čistočo.
KLJUČ 2 – organizacija sistema in ciljno vodenje
- Vzpostavitev učinkovitega sistema upravljanja, hierarhije od zgoraj navzdol.
- 5. stopnja: podjetje ima jasno strategijo in cilje. Cilji zaposlenih so usklajeni s cilji vodstva.
KLJUČ 3 – delo v delovnih skupinah
- Osredotočenost na skupinsko delo.
- Cilj sta sodelovanje zaposlenih in timsko delo.
- 5. stopnja: cilji so timsko delo, vsak zaposleni predlaga izboljšave.
KLJUČ 4 – zmanjšanje medfaznih zalog
- Cilj je razumevanje slabih učinkov prevelikih zalog.
- 5. stopnja: prilagodljiv sistem, da zadovolji kupca in proizvaja samo naročene izdelke.
KLJUČ 5 – hitre nastavitve
- Skrajševanje pretočnih časov, hitra prilagoditev procesov.
- 5. stopnja: hitre nastavitve so uvedene pri vseh strojih in procesih, pri drugih ključih vsaj 4. stopnja.
KLJUČ 6 – vrednostna analiza delovnih postopkov
- Cilj je skrajšati postopke, ki ne prispevajo k dodani vrednosti, in doseči boljšo produktivnost.
- 5. stopnja: uvajanje stalnih izboljšav v vse procese, pri drugih ključih vsaj 4. stopnja.
KLJUČ 7 – proizvodnja brez nadzora
- Cilj je proizvodnja brez napak in človeškega nadzora.
- 5. stopnja: z vzpostavitvijo proizvodnje brez nadzora smo uvedli avtomatizirani postopek in proizvodnjo brez napak.
KLJUČ 8 – povezovanje proizvodnih procesov
- Cilj je združitev procesov in oddelkov pri toku materiala in informacij.
- 5. stopnja: na sestankih so bile odstranjene ovire med procesi. Podjetje ima na tej stopnji hitro vzpostavljivo tehnologijo in se je sposobno prilagoditi spremembi.
KLJUČ 9 – vzdrževanje strojev in opreme
- Preventivno vzdrževanje opreme, boljša kakovost, večja produktivnost in manjši stroški zamenjave opreme.
- 5. stopnja: inovativno vzdrževanje v celotnem podjetju, izkoriščenost strojev 95 %, zaposleni obvladajo nastavitve; pri drugih ključih vsaj 4. stopnja.
KLJUČ 10 – disciplina na delovnem mestu
- Ključ je v motivaciji zaposlenih.
- Cilj je vzpostavitev trajnostne discipline na delovnem mestu in dobro delovno ozračje.
- 5. stopnja; delavci so zelo motivirani, prihajajo in odhajajo točno ter opravljajo dela, ki prispevajo k dodani vrednosti.
KLJUČ 11 – sistem zagotavljanja kakovosti
- Preventivno ugotavljanje kakovosti procesov.
- Cilj je proizvodnja brez nekakovostnih izdelkov ali proizvodnja brez napak.
- 5. stopnja: kupci so zadovoljni, uvedba sistemov poka yoke, izvržek manj kakor 0,1 %.
KLJUČ 12 – odnosi z dobavitelji
- Cilj je trajno sodelovanje z dobavitelji.
- 5. stopnja: dobavitelj je uvedel sistem 20 ključev in dosegli so vsaj 70 točk. Produktivnost se je podvojila, postali so prilagodljivejši.
KLJUČ 13 – odpravljanje vseh izgub
- Cilj je povečati produktivnost in učinkovitost.
- 5. stopnja: produktivnost, kakovost in dobavni roki so se izboljšali. Drugi ključi na 4. stopnji. Izkoriščenost dela je 95 %.
KLJUČ 14 – spodbujanje zaposlenih k izboljšavam
- Cilj je spodbujanje in pooblaščanje zaposlenih za izboljšave in ustvarjalne ideje.
- 5. stopnja: sistem izboljšav je napredoval, zaposleni sami uresničujejo ideje (zaposleni imajo npr. ustrezno znanje, da prilagodijo uporabnost strojev ipd.).
KLJUČ 15 – širjenje usposobljenosti zaposlenih
- Cilj je prožnost delavcev na različnih delovnih mestih in uspešno prilagajanje podjetja trgu.
- 5. stopnja: sposobnost prilagoditi se kupčevim zahtevam in spremembam na trgu.
KLJUČ 16 – načrtovanje proizvodnje
- Cilj je učinkovito načrtovanje proizvodnje in preverjanja procesov.
- 5. stopnja: naročeni izdelki so dobavljeni pravočasno, končni izdelki so kakovostni.
KLJUČ 17 – upravljanje učinkovitosti
- Cilj je povečati učinkovitost dela s stalnimi izboljšavami.
- 5. stopnja: cilji učinkovitosti so stvarni in spodbujajo zaposlene.
KLJUČ 18 – računalniška podpora vodstvu
- Cilj je povečanje zmogljivosti in večja podpora poslovanju, vpeljava informacijske tehnologije.
- 5. stopnja: uvedeni so sistemi, ki omogočajo pretok informacij od menedžmenta k proizvodnji in obratno ter med dobavitelji in partnerji.
KLJUČ 19 – varčevanje z energijo in materialom
- Cilj je razumeti smisel varčevanja z energijo in materialom ter varovanja okolja.
- 5. stopnja: z novimi tehnologijami je podjetje doseglo raven varčevanja z energijo in materialom. Zmanjšala se je poraba surovin zaradi reciklaže.
KLJUČ 20 – obvladovanje vodilnih tehnologij
- Cilj je biti tehnološko pred konkurenco, usposobiti zaposlene za uporabo najnovejše tehnologije.
- 5. stopnja: prevladuje uporaba najnovejše tehnologije in lastnega znanja. Vzpostavljen je prenos znanja iz generacije v generacijo.
Učinkovito uvajanje in uporaba metode 20 ključev lahko optimizirata število zaposlenih, ki dobro poznajo sodobne tehnologije, njihova delovna mesta so urejena, ni nepotrebnih stroškov z medfaznimi zalogami ali t. i. prekomerno proizvodnjo, med delavci vlada zaupanje, cenijo stalna usposabljanja in izobraževanje, vodstvo pa uživa podporo in preudarno ravna z doseženimi presežki ter delavce ustrezno nagrajuje.
Poka yoke
Poka yoke (jap. ポカヨケ, poka – napake, yokeru – izogibanje) je tehnika takojšnjega izločanja napak, ki nastanejo med procesom in so vzrok za neustrezen proizvod. Japonski inženir Šingo trdi, da »vzroki za neustrezne proizvode izhajajo predvsem iz delavčevih napak« [23]. »Škoda« torej nastaja sproti zaradi nenamernega početja, obrabe orodja, utrujenosti delavcev idr. Predvsem pa tehnika poka yoke upošteva, da smo ljudje zmotljiva bitja in občasno kaj pozabimo ali nenamerno storimo narobe. Ker se to lahko kaže v seriji izdelkov z napako, je Šingo predlagal, da se napake pregledujejo sproti oz. da se uvede sistem, ki bo delavcu omogočil sprotno preverjanje in tudi odpravo napak. Predlagal je tehnično rešitev, ki samodejno ugotovi napako, ustavi proces in zahteva takojšnjo odpravo pomanjkljivosti. To tehniko imenujemo poka yoke – sistem s takojšnjo povratno informacijo ugotovi ključni vzrok za napako in prepreči njeno ponovitev. Tako zagotovimo 100-odstotno preverjanje in brezhibno delovanje proizvodnega procesa. Za to se zahteva tudi sistemskost pri razvoju in prilagoditvi procesa.
Primer 45:
V proizvodnji, ki vključuje struženje sornikov, se pogosto obrabijo ali poškodujejo stružni noži. Sistem poka yoke, ki stalno preverja dolžino noža, takoj ko je dolžina nepravilna, to javi, ustavi proces in zahteva zamenjavo noža. Tudi ta se lahko izvede samodejno in s tem se prihranita neprecenljiv čas in denar pri preverjanju kakovosti končnih izdelkov. Brez tega sistema bi napako odkrili šele pri končnem izdelku ter porabili veliko časa in stroškov za odkrivanje njenega vzroka; ob tem bi nastalo tudi veliko izdelkov z napako, ki jih je treba bodisi popraviti ali zavreči. Oboje zahteva precejšnje stroške in čas.
Drugi primer prikazuje Slika 125 – z nastavkom (ang. Fixture) preprečimo napačno montažo. V proizvodnem procesu se namreč lahko zgodi, da se neki polizdelek med transportom obrne v napačno smer oz. da ga delavec pri ročnem vstavljanje vstavi z napačne strani. Preprost mehanski pripomoček lahko prepreči napačno vstavitev.
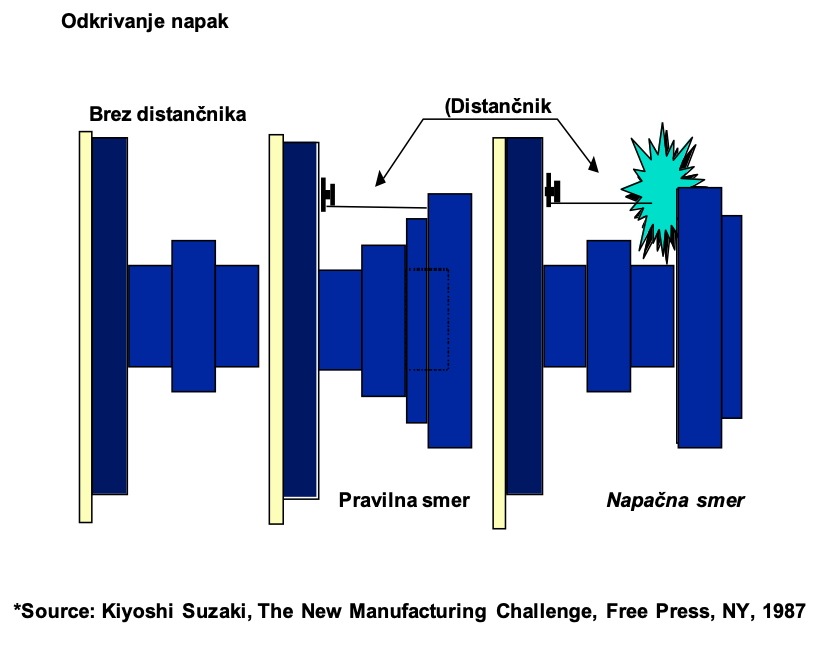
Sistem poka yoke zagotavlja odpravljanje napak že v samem procesu in omogoči proizvodnjo skoraj brez njih. Tako se lahko izognemo zamudnemu in sistemskemu iskanju napak v končnem izdelku in dodatnim stroškom za popravilo. Toyotin proizvodni sistem, ki je uvedel poka yoke, je s to revolucionarno tehniko občutno zmanjšal stroške končnega preizkušanja in število napačno narejenih izdelkov, s tem pa tudi končno ceno. Poka yoke je teoretično uporaben na vseh ravneh proizvodno-storitvenih dejavnosti in je dober način zniževanja stroškov kakovosti.
Jidoka
Jidoka (jap. 自働化, ji se nanaša na delavca, ki je naredil nekaj narobe, do je proces, delo, ka pa le pripona) pomeni samostojno, samodejno delo s pomočjo človeka [24] – samodejni sistem, ki deluje pod človekovim nadzorom. To tehniko je v svoj proizvodni sistem uvedla Toyota; v proizvodnji, ki sicer poteka samodejno, občasno prihaja do nenormalnih okoliščin in tedaj ukrepa človek. Jidoka uvaja v samodejni sistem več nadzornih kakor proizvodnih funkcij: človek v nadzorni funkciji ob nastopu nenormalnih okoliščin prekine samodejno proizvodnjo in po potrebi posreduje do rešitve problema, da se prepreči nastanek izdelkov z napako. Pri tem seveda dodatno razišče vzrok in poskrbi, da se ista napaka ne ponovi. Tehnika jidoka zelo dobro dopolnjuje sistem poka yoke.
Primer 46:
V trenutku zaznave napake/problema človek ustavi proizvodni sistem in obvesti o tem nadzor. Informacija o zaustavitvi je vidna na semaforju (andonu), dokler napake ne odpravijo. Taka zaustavitev prepreči proizvajanje izdelkov z napako, ki bi jih pozneje zavrgli ali popravljali. Pri tem bi nas pestile težave in stroški z ugotovitvijo vzroka za nastanek napake. Ko je napaka v proizvodnji odpravljena, se semafor sprosti in proizvodnja se nadaljuje.
Kanban
Kanban (jap. 看板, kan – kartica, ban – signal) je japonska beseda za »kartico«, »vstopnico«, »oznako«, tehnika pa sodi med pomembno orodje menedžmenta za tok surovin, proizvodnih delov, naročil in sestavljalnih procesov [25]. V nasprotju s centraliziranim vodenjem proizvodnje, pri katerem posamezne enote nimajo nobenega vpliva na naročanje surovin in polizdelkov, sistem kanban ne potrebuje velikih zalog in skladiščenja ter je zelo prilagodljiv, če se razmere na trgu spremenijo.
Sistem kanban pa ni primeren za specializirana naročila ali manjšo proizvodnjo, ker je standardizacija proizvodnega programa v tem primeru pravzaprav nemogoča.
Vsaka kartica kanban (Slika 126) vsebuje podatke o materialu, naročniku in dobavitelju, številu kosov, številki materiala in skladišču ter ima svojo zaporedno številko, ki je enaka številki, vneseni v informacijski sistem.
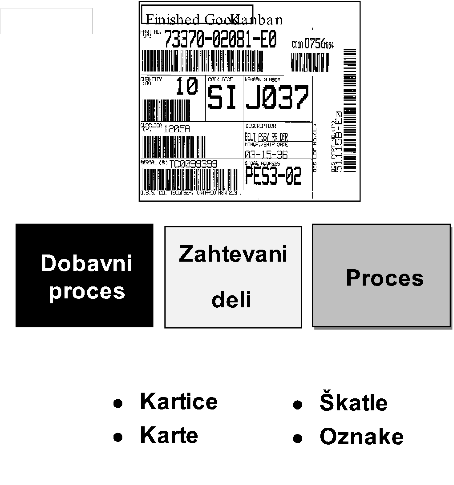
Primer 47:
Materialni tok v Toyotinem proizvodnem obratu (Slika 127). Ko se zaloge zmanjšajo, operater »prenese« listič kanban z vsemi podatki o potrebnem materialu k dobavitelju procesa (proizvajalec, drug proizvodni proces). Dobavitelj prevzame listič, dobavi zahtevani material iz svojega skladišča in izpolni svoj kanban, v katerega zapiše, koliko materiala je bilo predano iz skladišča. Tak kanban potuje naprej do operaterja, ki tako natančno izve, kaj je bilo predano iz skladišča, in sproži dobavo oz. proizvodnjo dobavljenega materiala.
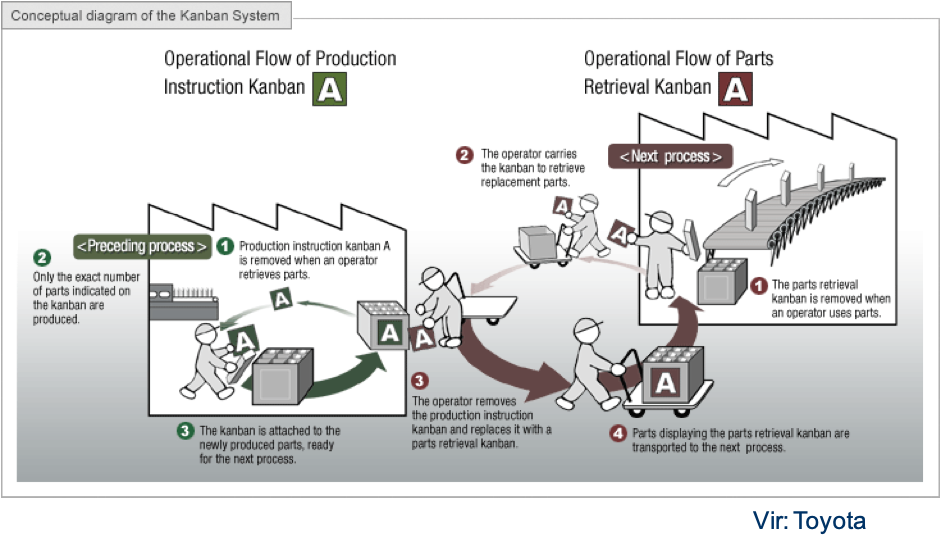
S sistemom kanban lahko optimiziramo materialni tok tako, da pravočasno zagotavljamo ves material za nemoteno proizvodnjo, hkrati pa ne kopičimo zalog v oddaljenih skladiščih, ker je to povezano z velikimi stroški. Če so dobavitelji manj zanesljivi, lahko z uporabo tega sistema organiziramo tudi t. i. vmesno (prehodno) skladišče ali pa skladiščenje prepustimo zunanjemu izvajalcu in ga vključimo v sistem kanban. Ta sistem je tudi ena od osnov vitke (ang. lean) proizvodnje z minimalnimi zalogami, pravočasno dobavo in dokaj nizkimi stroški glede na centralizirano vodenje materialnega toka.
Primer vitke proizvodnje
Dober primer vitke proizvodnje je Toyotin proizvodni sistem TPS (ang. Toyota Production System), čigar avto je Taiči Ohno [25], nekoč direktor tovarne Toyota, po poklicu inženir:
- temelji na odstranjevanju sedmih vrst izgub;
- proizvodnja le v zahtevani količini in v določenem času (ang. Just in Time); prevelika količina je čista izguba;
- ker napake odstranjujemo sproti (jidoka, poka yoke), ne potrebujemo oddelka za končno preverjanje kakovosti izdelkov;
- tovarna je organizirana po načinu celic s semaforjem (andon) – ta sporoča naslednji celici, ali je s polizdelkom vse v redu;
- celoten proizvodni proces teče v skladu s prodajo – enako hitro, kot teče prodaja, teče tudi proizvodnja;
- izpolnjevanje zgornjega merila vodi do vitke proizvodnje;
- proizvodnja brez izvržka (jap. muda) in brez izgub zaradi prepoznave pomanjkljivosti in njihove takojšnje odprave;
- odprava opravil brez dodane vrednosti.