4.3. Opredelitev problema
Imre Cikajlo and Franc Gider
Če smo se ob metodi simpleks doslej spoznavali s problemi in sestavljali mozaik s podatki, ki opisujejo problem in sposobnosti procesa, bo treba v nadaljevanju poiskati vzroke za nastanek problemov.
Pri tem se osredotočimo na iskanje glavnih vzrokov, torej povzročiteljev problema. Pogosto iščemo tudi vzroke, ki ovirajo učinkovitost procesa. Toda pozorni moramo biti na raven reševanja problema, saj je ta velikokrat zelo zapleten in vsaka nadaljnja neprimerna rešitev bi nakopičila nove probleme. Zato kompleksne probleme razbijemo, razčlenimo v manjše, preprostejše, tako pa lažje, hitreje in z manj stroški pridemo do rešitve. Pomagamo si s številnimi tehnikami za razčlenitev, iskanje in ovrednotenje vzrokov ter opredelitev pomembnih vzrokov, ki s svojo pogostnostjo največ prispevajo k neučinkovitosti procesa:
- razčlenitev problema (ang. Drill Down),
- 5-krat zakaj (ang. 5 Why),
- diagram vzrokov in posledic (ang. C&E Diagram),
- matrika vzrokov in posledic (ang. C&E Matrix),
- analiza moči in vplivov (ang. Force Field Analysis),
- kontrolni listi (ang. Checksheets),
- grafi (ang. Graphs),
- histogrami (ang. Histograms),
- Paretov diagram (ang. Pareto Chart).
Razčlenitev problema
Razčlenitev problema (ang. Drill Down) uporabljamo zato, da velik, zapleten problem razbijemo na več manjših. Manjši problemi zadevajo nižjo raven problema in so kot taki pogosto enostavneje rešljivi, zato jih tudi lahko obravnavamo ločeno. Razčlenitev z vprašanji nam daje možnost, da na problem gledamo iz drugega zornega kota in dobimo boljšo predstavo o vseh okoliščinah. Prav tako nam pomaga odkriti in razumeti dejavnike, med njimi vzroke za nastanek problema. Razčlenjevanje nas privede do informacij, ki jih do nedavnega nismo niti povezovali z nastalim problemom in ki nato sprožijo nove ideje.
Postopek razčlenjevanja problema
- Razčlenitev začnemo tako, da problem napišemo na levo stran velikega lista papirja.
- Desno od problema napišemo točke, ki predstavljajo njegovo nižjo raven. Te točke nam dajejo informacijo o problemu in iztočnice za nadaljnje ideje.
- Proces nadaljujemo tako dolgo, dokler ne pridemo do smiselnih zaključkov.
- Včasih točk ne moremo kar napisati. V takih primerih je treba izvesti poglobljeno raziskavo.
Primer 17:
Lastnik jadralnega kluba ima problem, ker se člani pritožujejo nad slabo kakovostjo vode v okolici kluba. Zato je razčlenil problem (Slika 50):
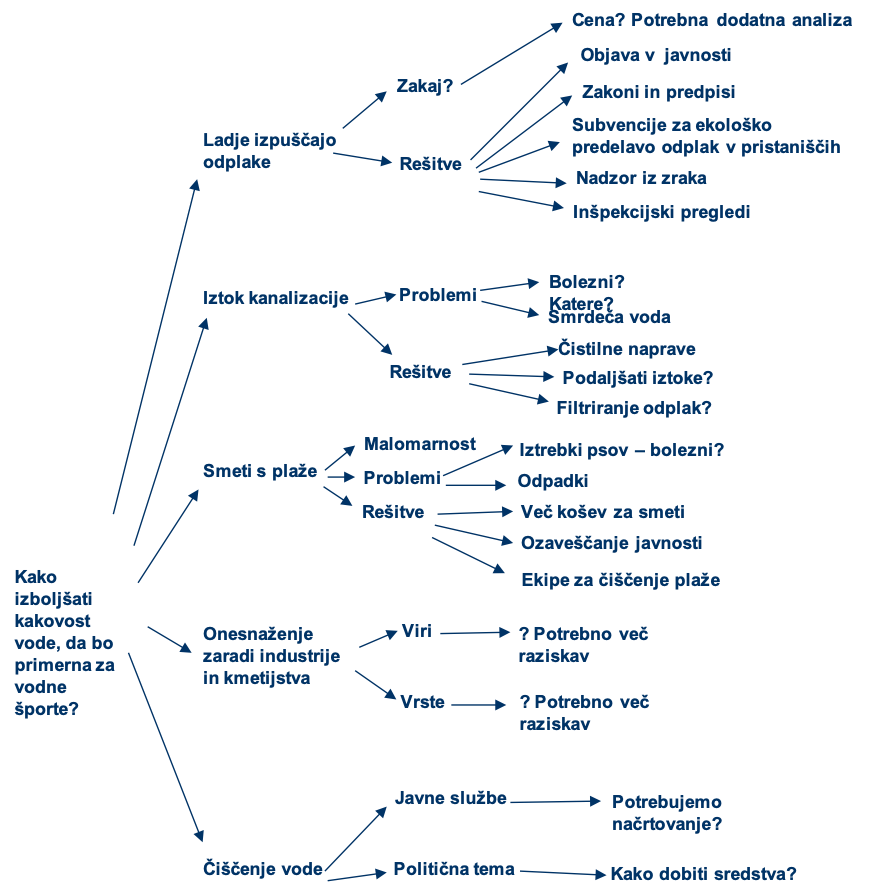
5-krat zakaj
Zakaj je vprašanje, ki si ga moramo pogosto zastaviti, če se ukvarjamo z reševanjem problemov ali iščemo nove ideje in rešitve. Tehnika »5-krat zakaj« (ang. 5 Why) sodi med pomembno orodje 6 sigma [12], [13] Zakaj petkrat? To je še eno vprašanje več. Število pet se pogosto omenja kot pravilo (ang. Five is a good rule of thumb).
Namen tehnike »5-krat zakaj« je ugotoviti glavni vzrok problema v našem procesu. Prvotnega vzroka pogosto ni preprosto ugotoviti, postopek je lahko dolgotrajen in zapleten, še posebej, če uporabljamo statistične metode analize. S tehniko »5-krat zakaj« lahko določimo povezave med prepoznanimi vzroki, ki so možni povzročitelji problema, in se tako izognemo dodatni analizi. Prav zaradi svoje enostavnosti sodi ta tehnika med preprostejše in pogosteje uporabljene tehnike za določitev problema. Uporabljamo jo:
- za reševanje problemov, v katerih nastopi človeški dejavnik oz. je posredni vzrok za njihov nastanek človek,
- v poslovnem svetu, kjer sprejemamo odločitve,
- za izboljšanje kakovosti procesov z orodjem 6 sigma.
Postopek za izvedbo »5-krat zakaj«
- Izpišemo problem, ki ga obravnavamo. Pomembno je, da ga oblikujemo in dobro opišemo; tako se lahko skupina dobro osredotoči na bistvo problema.
- Postavimo vprašanje, zakaj se je problem pojavil, in zapišemo odgovor.
- Če je prejšnji odgovor nezadovoljiv, vprašanje ponovimo.
- Vrnemo se k 3. koraku in ponovimo vprašanje, odgovor pa zapišemo. Postopek ponavljamo, dokler skupina ne doseže soglasja o vzroku za nastanek problema. Postopek lahko ponovimo tudi z več kakor petimi zakaji.
Vsak problem se kaže z nekaterimi simptomi. Rešimo ga lahko na dva načina: tako da odpravimo simptome ali pa vzroke za simptome (npr. pri glavobolu s tableto proti bolečini odpravimo samo simptom, ne pa vzroka glavobola). Tehnika »5-krat zakaj« nam pomaga odkriti vzroke, ki jih moramo odpraviti, če hočemo problem trajno rešiti. V primeru (Slika 51) raziščimo in lokalizirajmo problem pri pregoreli varovalki.
Primer 18:
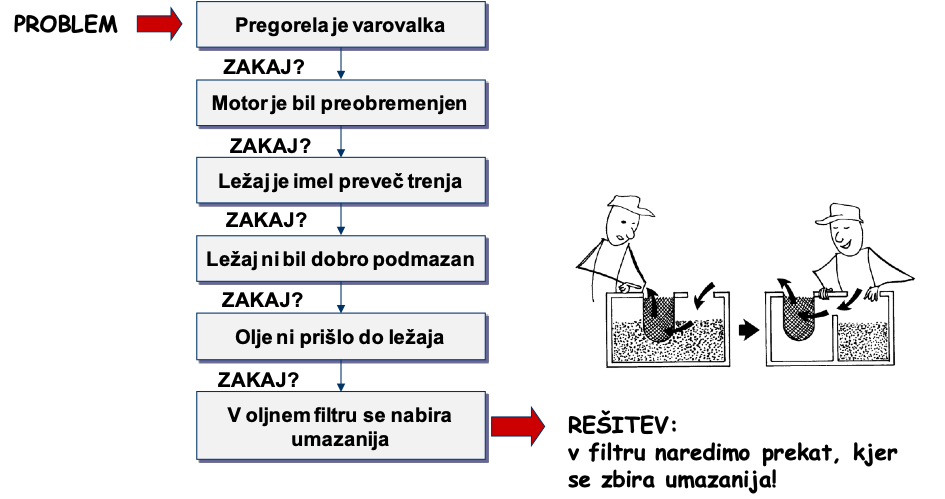
Iz primera (Slika 51) je razvidno, da končni zakaj privede do prvotnega vzroka za problem. Taka rešitev je dokaj preprosta. Če poenostavimo: veliko bolj učinkovito je s petimi preverjanji ugotoviti glavni vzrok za problem, ki je po navadi hitro rešljiv, kakor iskati rešitve, s katerimi bi odpravljali posledice (simptome). Če bi samo zamenjali varovalko in ne bi preuredili filtra, bi se problem v najkrajšem možnem času ponovil.
Zakaj-zakaj
Tehnika zakaj-zakaj je na las podobna tehniki »5-krat zakaj«, toda dopušča možnost, da ima eno vprašanje zakaj več možnih odgovorov. Vsak odgovor analiziramo naprej z novim vprašanjem zakaj. Ko menimo, da je odgovor dovolj preprost in da imamo zanj tudi rešitev, izpraševanje končamo. Tako razširjena tehnika omogoča boljšo razčlenitev problema in delno reševanje z odpravljanjem lokalnih vzrokov.
Primer 19:
Razčlenitev problema v zvezi s polizdelki, ki bi morali biti ogrevani pri prehodu v nadaljnji proces, a prihajajo hladni (Slika 52):
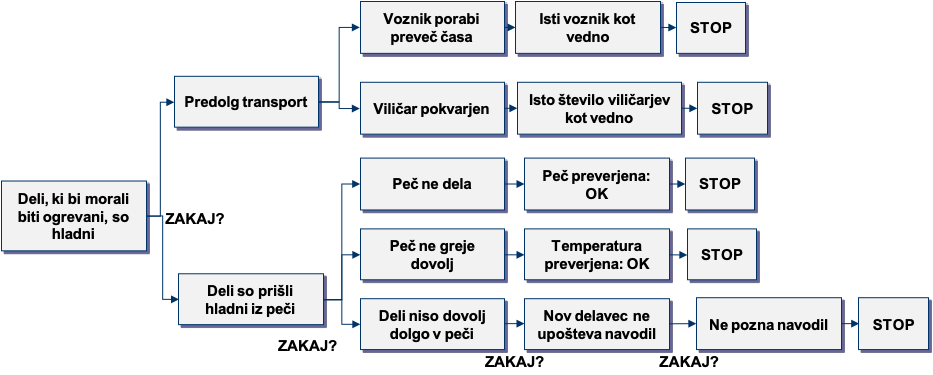
Diagram vzrokov in posledic
Diagram vzrokov in posledic (ang. Cause&Effects Diagram, C&E Diagram) je orodje, s katerim tim grafično predstavi vse s problemom povezane vzroke, ki mu jih je uspelo določiti. Namen diagrama je odkriti ključne vzroke posebnega problema; večina vzrokov namreč ni neodvisna, temveč so medsebojno odvisni, torej med njimi obstajajo nekatere povezave.
Pogosto diagram vzrokov in posledic imenujemo Išikavov diagram (imenovan po Kausu Išikavi, ki je uporabil tehniko že leta 1960) ali diagram ribja kost, ker je njegova oblika zelo podobna ribji kosti (Slika 53). Z njim poiščemo vzroke za probleme in ne le simptomov. Celoten tim je usmerjen na iskanje dejanskih vzrokov, ki so razdeljeni na: človek, stroj, material, metode.
Tim se dogovori o zastavljenem problemu, ki je bil predhodno ugotovljen, in ga napiše na levo stran diagrama (Slika 53). Pomembno je, da vsi člani tima problem razumejo in se z njim strinjajo. Na desno narišemo diagram v obliki ribje kosti – vsaka kost predstavlja eno vrsto vzrokov. Tim ugotavlja vzroke z uporabo orodja, npr. možganske nevihte (ang. Brainstorming). Iščemo lahko ožje vzroke, ki jih potem razvrstimo, ali pa najprej določimo kategorije in potem iščemo ožje vzroke. Težko je določiti, kateri postopek je »pravilnejši«, saj se nekateri vzroki pojavljajo pri več kategorijah (dejavnikih). To so pomembni ali ključni vzroki.
Pri razvrščanju vzrokov v kategorije oz. predhodnem določanju kategorij moramo upoštevati čim več dejavnikov, ki na problem vplivajo:
- v proizvodnih procesih so običajni dejavniki 4M (ang. man, machine, material, method – človek, stroj, material, metoda),
- v storitvenih procesih pa najpogosteje: politika, postopki, prostor, oprema, okolje in ljudje.
Postopek načrtovanja diagrama vzrokov in posledic
- Opredelitev problema (zapišemo v kvadrat na levi strani lista in narišemo »ribjo hrbtenico«).
- Iskanje glavnih dejavnikov za problem (narišemo »kosti« iz »hrbtenice«). Uporabimo dejavnike 4M za proizvodne ali druge dejavnike za storitvene procese.
- Iskanje vzrokov po glavnih dejavnikih (črte so »ribje kosti«).
- Analiza diagrama (iskanje najverjetnejšega vzroka za problem). Glasovanje za posamezne vzroke (vsi člani skupine glasujejo za vzroke, ki so po njihovem najpomembnejši):
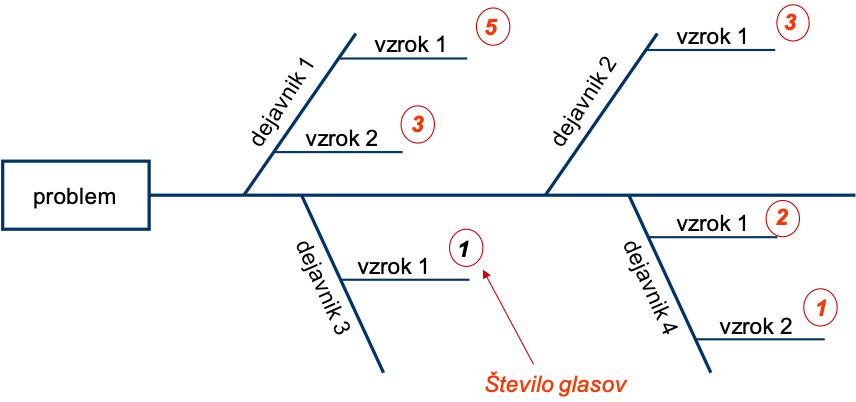
Primer 20:
Menedžer trgovskega podjetja raziskuje, zakaj je ena od poslovnih enot neuspešna. Naredi diagram ribja kost (Slika 54):
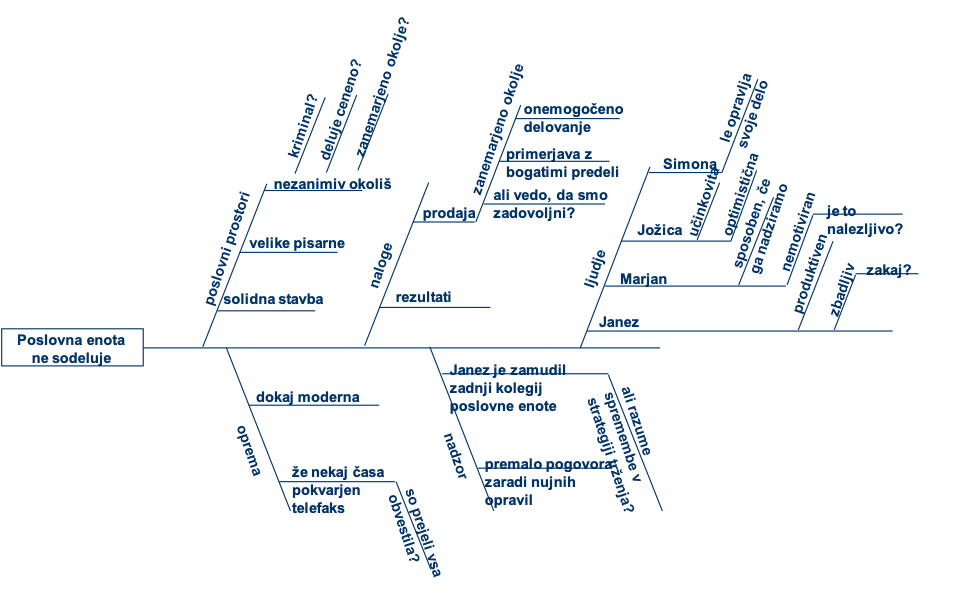
Matrika vzrokov in posledic
Na podlagi diagrama vzrokov in posledic dobimo seznam možnih vzrokov za problem (tudi do 50), z uporabo matrike pa jim določimo težo in pomembnost (prioriteto). Matrika vzrokov in posledic (ang. Cause&Effects Matrix, C&E Matrix) je orodje, s katerim poiščemo povezave med prepoznanimi vzroki in posledicami, ki jih ti vzroki povzročijo. Namen orodja je določiti pomembnost posameznih vzrokov. To je važno, saj niso vsi nujno povezani z vsakim problemom oz. imajo na posamezne probleme različen vpliv. Z matriko vzrokov in posledic tako lahko določimo stopnjo odvisnosti med ugotovljenimi vzroki in problemi, ki smo jih izpostavili..
Postopek izdelave matrike vzrokov in posledic:
- vzroke razvrstimo po teži, nato pa se odločimo, katere bomo odpravljali najprej;
- v vrstice zapišemo vzroke;
- v stolpce zapišemo probleme in vsakega ocenimo glede na pomembnost;
- v vsako celico matrike vpišemo vpliv vzroka na problem (korelacijo med vzrokom in posledico). Uporabimo lestvico od 1 do 10, a ne več kakor 4 stopnje (npr. 0, 1, 3, 9);
- vzroke razvrstimo tako, da v vsaki vrstici seštejemo zmnožke posameznih korelacij in pomembnosti problemov (Slika 55).
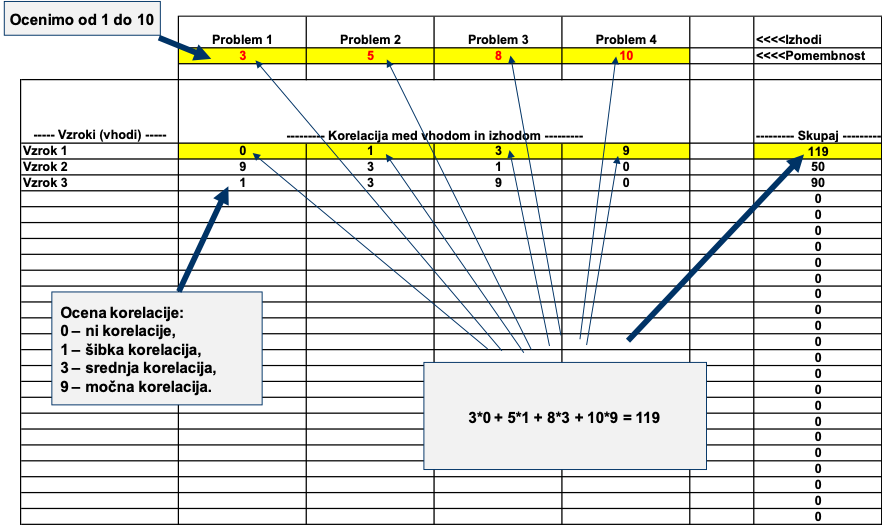
Primer 21:
Raziščimo primer sestavljanja računalnikov z izbrano programsko opremo in pravočasno dostavo. Najpomembnejše za naročnika je seveda delovanje naročene opreme, ključni pa sta tudi programska oprema in pravočasna dostava. Manj pomembna, a ne nepomembna je še možnost nadgradnje, najmanj pomembni pa so dostopnost priključkov, samo ohišje, odpiranje pokrova omarice in glasnost delovanja.
Slika 56 prikazuje matriko vzrokov in posledic, iz katere je razvidno, da je kritično predvsem nameščanje programske opreme in izbira oz. vstavljanje večjih enot, kakršna sta procesor s hladilnikom in diskovni pogoni. Iz rezultatov lahko sklepamo, da moramo v procesu bolj nadzorovati nameščanje programske opreme oz. posodobiti preizkušanje, ki bo odkrilo morebitne napake, ter izboljšati sistem za izbiro procesorja in diskovnih pogonov, pa tudi njihovo nameščanje (prava velikost, tip in izbrana znamka).
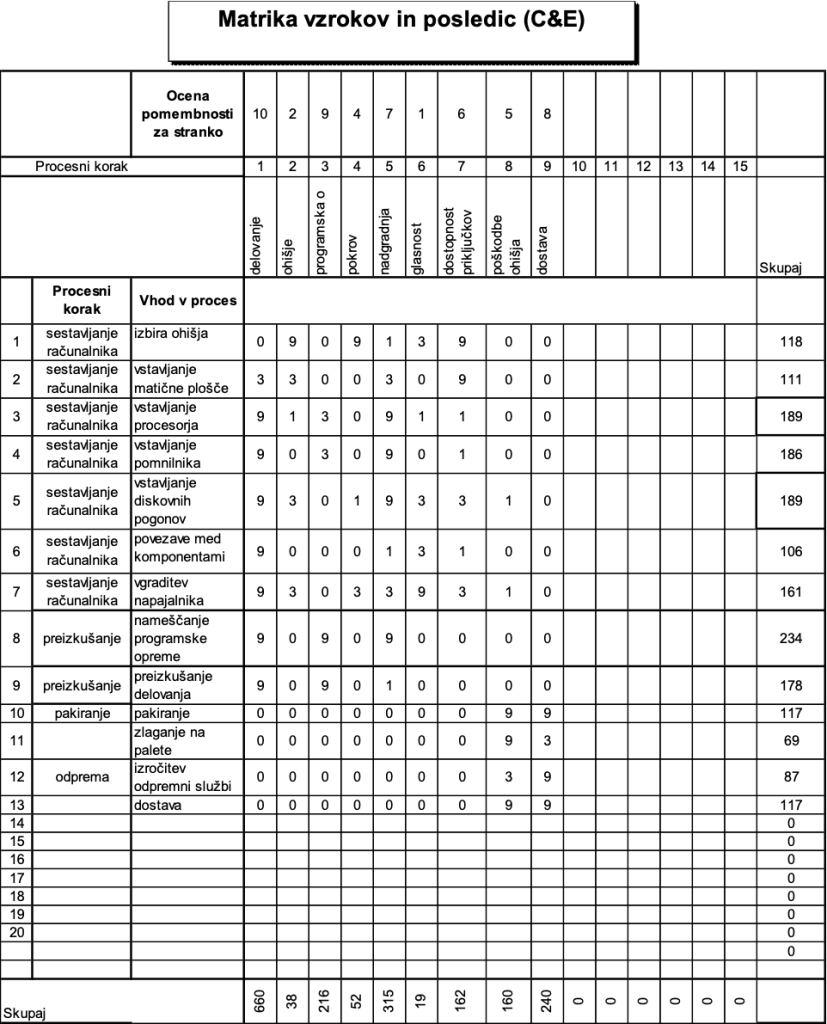
Analiza moči in vplivov
Analizo moči in vplivov (ang. Force Field Analysis) je razvil Kurt Lewin. Orodje lajša razumevanje ter presojo vplivov in dejavnikov, ki podpirajo posebne rešitve problema oz. ideje ali jim nasprotujejo. Namen orodja je povečati zaupanje v pozitivne rešitve problema in zmanjšati negativne vplive oz. sile proti spremembi (Slika 57). Določimo sile, ki so za (+) spremembo obstoječega stanja, in tiste, ki so proti (–) spremembi.
Na podlagi analize vplivov in moči ugotovimo sile, na katere se moramo osredotočiti, če hočemo spremeniti stanje:
- določimo predmet razprave oz. problem, ki ga rešujemo, in zadani cilj;
- v skupini poskušamo prepoznati sile za spremembo in jih napišemo na levo stran;
- v skupini poskušamo prepoznati sile proti spremembi in jih napišemo na desno stran;
- prednostno razvrstimo sile za spremembo, ki podpirajo rešitev problema, in sile proti spremembi za poznejšo uporabo tehnik vrednotenja idej.
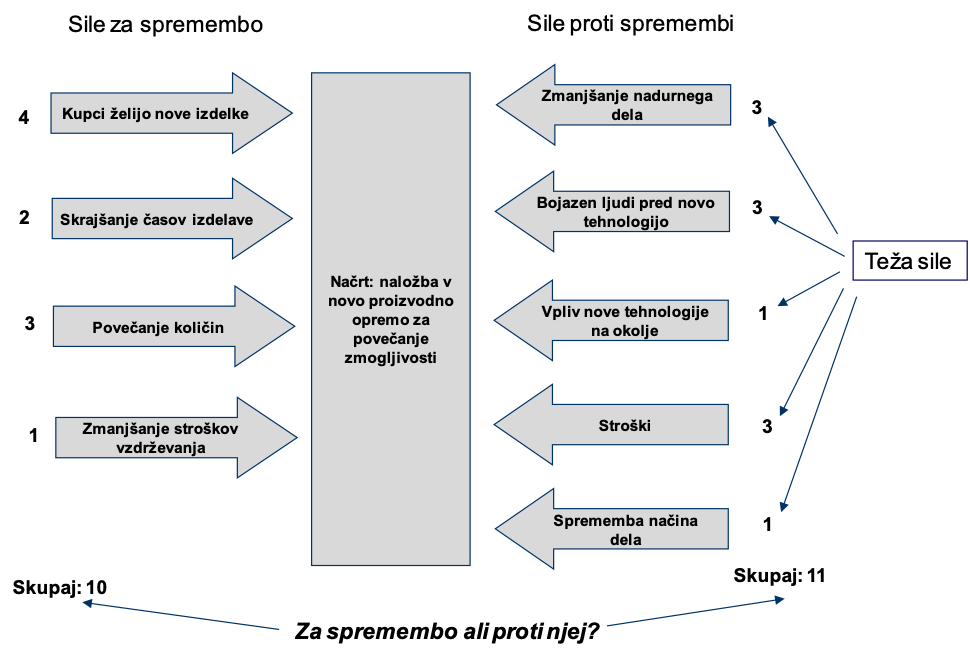
Dajanje prednosti silam za spremembo ni vedno najboljša rešitev problema. Pogosto se zgodi, da odpravljanje negativnih sil bistveno več prispeva k iskanju prave rešitve.
Kontrolni listi
Na kontrolne liste (ang. Checksheets) pogosto naletimo tudi pod imenom evidenčni listi in se v praksi kažejo kot zelo uporabne oblike zajemanja podatkov. Sistematično vnašanje podatkov, ki smo jih dobili z meritvami v procesu ali iz procesnih poročil, po obdobjih nam daje pregled nad procesom:
- boljše razumevanje procesnih podatkov,
- podatki kažejo objektivno stanje, ne subjektivnega ugibanja,
- spodbuda k dobremu določanju dogodkov in stanj procesa,
- pregled nad trenutnim stanjem procesa na podlagi dejanskih meritev, informacij.
Kontrolni list oblikujemo tako, da pridobimo podatke o vzrokih za probleme, ki nas zanimajo. Z njim opazujemo proces določen čas, zapisujemo podatke in nato ugotovimo vzrok za problem, ki ga kaže najprej odpraviti. Postopek priprave kontrolnih listov:
- naredimo seznam dogodkov oz. stanj procesa, ki jih bomo opazovali,
- določimo odgovorne za zbiranje podatkov ter časovni okvir in vire,
- predlagamo obliko in način zapisovanje kontrolnih listov, npr. imena dogodkov, časovne in vsebinske informacije (Slika 58),
- k zbiranju informacij spodbudimo celoten tim, tudi menedžersko ekipo, tako da dosežemo nedvoumnost in točnost podatkov.
Primer 22:
Podjetje, ki proizvaja sestavljive otroške igrače, je en mesec analiziralo reklamacije kupcev. Vzroke za reklamacijo je razdelilo na pet vrst: napaka pri naročilu, napaka pri odpremi blaga, napačno izdan račun, poškodba igrače in poškodba embalaže. Naredilo je spodnji kontrolni list. Z njega je na koncu meseca razbralo, da je bilo največ reklamacij zaradi embalaže, sledita pa postopek naročanja in poškodba izdelka.
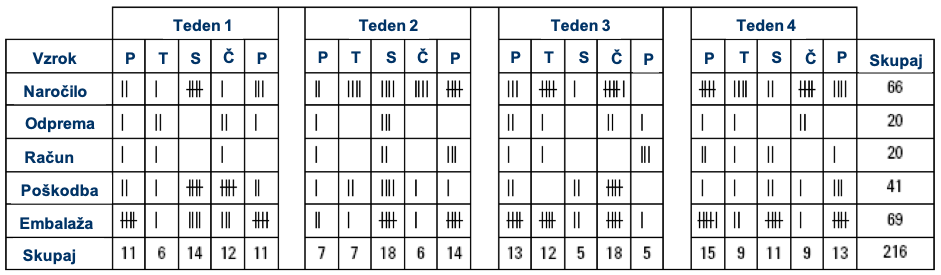
Grafi
Grafe (ang. Graphs) uporabljamo za grafično predstavitev zbranih podatkov, ki jih združujemo v informacije. Informacija je namreč skupek obdelanih podatkov, ki ima svoj pomen, tega pa lažje razberemo, če so zbrani podatki predstavljeni v nazorni, enostavni obliki. Najprimernejše oblike so stolpčni graf, linijski graf in razsevni (ang. scatter) diagram. Za prikaz deleža posameznih vzrokov pa je najboljši tortni diagram (ang. Pie Chart, Slika 59).
Po splošni definiciji je graf množica objektov, točk, vozlišč ali vozlov, ki so medsebojno povezani s črtami, robovi ali vejami. Lastnosti grafov obravnava teorija grafov, s katero lahko razberemo povezave, odvisnosti med količinami, potek nekega pojava … Grafi so opremljeni s številčnimi podatki, ki predstavljajo absolutno vrednost, številsko vrednost napak, pogostnost vzrokov, časovni parameter ali odstotek vseh možnih vrednosti, npr. vzrokov.
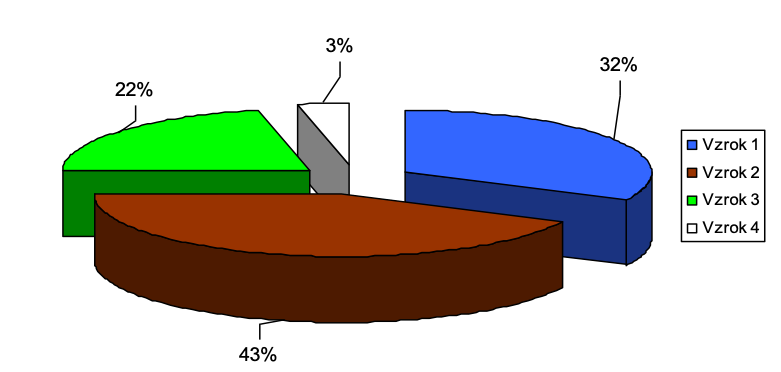
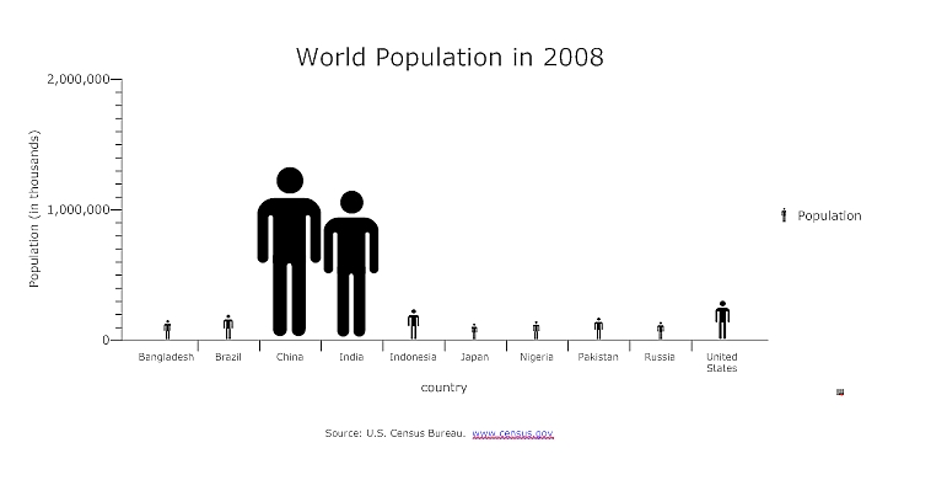
Pri reševanju problemov pogosto posegamo po stolpčnih grafih in tortnih diagramih (Slika 59). V njih predstavimo podatke, zbrane s kontrolnimi kartami, ali matriko vzrokov in posledic. Tako lahko razdelamo in prikažemo, kolikšen je delež posameznih vzrokov, problemov ali delež zbranih idej, ki jih želimo uveljaviti za reševanje posameznega problema (Slika 60).
Histogrami
Pri večkratnem pojavljanju enakih idej, problemov ali rešitev oziroma podatkov se srečamo s pojmom pogostnost. Podatke, rešitve, probleme in ideje združujemo v kategorije glede na izbrana merila. Pri numeričnih podatkih sta to spodnja in zgornja meja sprejemljivosti oz. tolerance. Če vse vrednosti, ki smo jih uvrstili v posamezne kategorije, preštejemo, dobimo informacijo o pogostnosti ali frekvenci. Pogostnostno razporeditev grafično prikažemo s pogostnostnim diagramom ali histogramom (ang. Histogram). Ta nam tudi ponuja statično sliko procesa. Histogram (Slika 61) dobimo s prikazom pogostnosti podatkov v stolpcu nad vsako od kategorij. Višina stolpca torej prikazuje pogostnost kategorije.
Histogram se uporablja za prikaz distribucije podatkov in iz njega lahko sklepamo o njihovi naravi. Navadno ga uporabljamo za predstavitev sposobnosti procesa zadostiti zahtevam kupcev. Pri reševanju problemov pogosto iščemo vzroke za številne težave, ugotovljene vzroke razvrstimo v kategorije in spremljamo njihovo pogostnost (Slika 61). Najpogostejših povzročiteljev problemov se tako lahko lotimo nemudoma in jih poskušamo odpraviti čim prej.
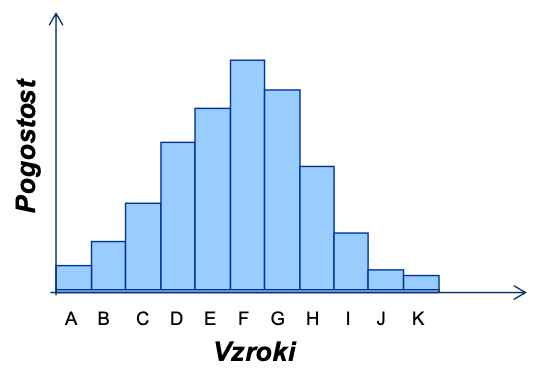
Primer 23:
Z uporabo kontrolnega lista (Slika 62), tortnega diagrama (Slika 63) in histograma analiziramo spodnji primer. Podatke za posamezne dneve si izmislimo.
Podjetje, ki se ukvarja z distribucijo kruha, je pregledalo reklamacije v preteklem mesecu in odkrilo, da so bili najpogostejši vzroki zanje prepozna dostava, nepravilna količina, poškodovan oz. pokvarjen kruh in neprijaznost osebja. Podjetje se je zato odločilo, da bo en mesec spremljalo vse reklamacije in na tej podlagi pripravilo ukrepe za izboljšanje stanja.
P | T | S | C | P | P | T | S | C | P | |
---|---|---|---|---|---|---|---|---|---|---|
PREPOZNA DOSTAVA | 2 | 0 | 1 | 1 | 3 | 3 | 1 | 0 | 2 | 1 |
NEPRAVILNA KOLIČINA | 1 | 1 | 2 | 1 | 0 | 2 | 1 | 1 | 3 | |
POŠKODOVAN KRUH | 0 | 0 | 2 | 1 | 5 | 1 | 0 | 0 | 3 | 1 |
POKVARJEN KRUH | 1 | 0 | 0 | 0 | 0 | 2 | 1 | 0 | 4 | 3 |
NEPRIJAZNOST OSEBJA | 1 | 2 | 1 | 0 | 3 | 7 | 3 | 1 | 0 | 0 |
P | T | S | C | P | P | T | S | C | P | VSOTA | % | |
---|---|---|---|---|---|---|---|---|---|---|---|---|
PREPOZNA DOSTAVA | 4 | 1 | 0 | 2 | 1 | 7 | 3 | 0 | 7 | 1 | 40 | 23.3% |
NEPRAVILNA KOLIČINA | 2 | 2 | 0 | 2 | 8 | 0 | 0 | 2 | 1 | 0 | 29 | 16.9% |
POŠKODOVAN KRUH | 0 | 1 | 2 | 3 | 0 | 2 | 0 | 1 | 2 | 3 | 27 | 15.7% |
POKVARJEN KRUH | 0 | 4 | 5 | 8 | 2 | 6 | 1 | 1 | 3 | 0 | 41 | 23.8% |
NEPRIJAZNOST OSEBJA | 3 | 1 | 0 | 1 | 4 | 2 | 1 | 0 | 2 | 3 | 35 | 20.3% |
SKUPAJ | 172 | 100% |
Slika 62. Kontrolni list za obdobje štirih tednov v podjetju za distribucijo kruha
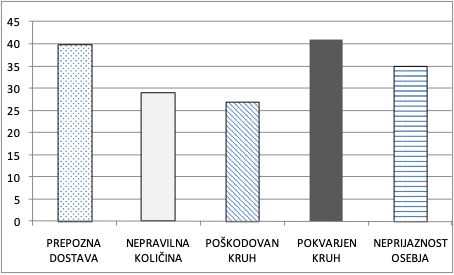
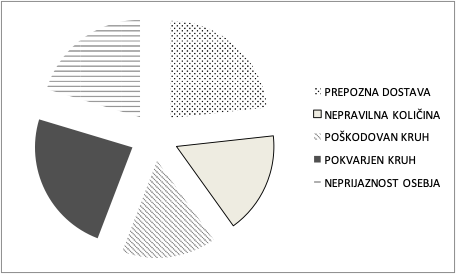
Paretov diagram
Vilfredo Pareto (1848–1923) je bil italijanski ekonomist, ki je raziskoval porazdelitev bogastva v Italiji v 19. stoletju. Ugotovil je, da je v takratni družbi – in tudi sicer – veljalo pravilo, da je večina bogastva v lasti manjšega dela prebivalstva, kar je znano tudi kot 10/90 (oz. 20/80). Ta trditev pomeni, da je 90 (80) % bogastva v rokah 10 (20) % prebivalstva, če pa jo prenesemo v reševanje problemov, pomeni, da 20 % vzrokov povzroči 80 % vseh problemov. Iz tega je nastal Paretov diagram – stolpčni diagram, ki prikazuje, kako pogosto se pojavi neka vrsta razlogov za problem [16].
Paretov diagram (ang. Pareto Chart) uporabljamo za prepoznavo najpomembnejših vzrokov, ki povzročajo večino problemov v procesu.
Zakaj ga uporabljamo? Prednosti njegove uporabe so v tem, da vidimo, kateri vzroki imajo največji delež pri problemu. Osredotočimo se na tiste vzroke, ki največ prispevajo k problemu oz. katerih izboljšanje bo dalo največje učinke.
Sestavljanje Paretovega diagrama:
- izberemo vzroke, ki jih bomo opazovali z eno od metod za zbiranje idej (možganska nevihta, zapisovanje idej …),
- določimo enoto merjenja: količinsko, stroškovno …,
- določimo obdobje za zbiranje podatkov o procesu,
- podatke grafično predstavimo v obliki histograma.
Abscisa Paretovega diagrama (Slika 64) predstavlja »vzroke za nastali problem«. Začnemo s tistim, ki ima največjo pogostnost oz. je vrednostno najpomembnejši, nato pa padajoče po velikosti razvrstimo manj pogoste vzroke za problem.
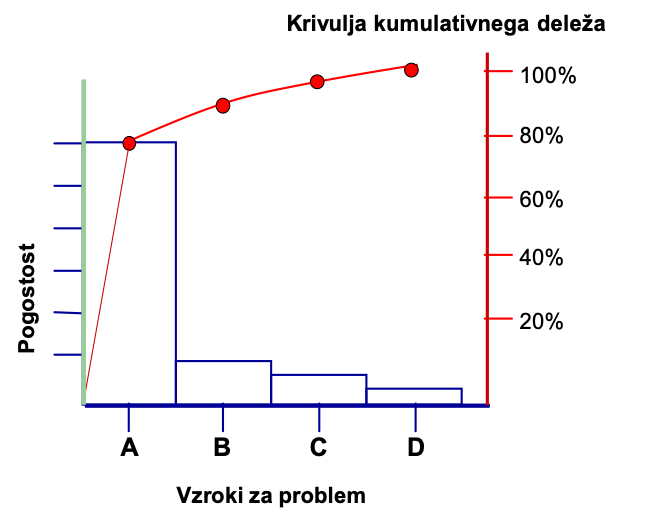
Iz Paretovega diagrama je razvidno, na katere napake se moramo osredotočiti, če želimo kar najbolj zmanjšati problem oz. povečati učinkovitost procesa. Paretovo pravilo: 20 % vzrokov povzroči 80 % problemov (Slika 65), pomeni, da je količina prizadevanja in stroškov, vloženih v odpravljanje vzrokov za nastali problem, najmanjša, če odpravimo vzroke, ki povzročijo večji del problema (ponavadi so to eden do trije vzroki). Vzroke, ki povzročijo minimum problemov, lahko nemalokrat izpustimo, tako pa racionaliziramo povečanje učinkovitosti procesa.
Paretov diagram je primeren tudi za izboljšanje kakovosti storitvenih dejavnosti. Tako kot vzroke upoštevamo reklamacije, pritožbe, povzročitelje stroškov, neustrezne dobave, vzroke, ki vplivajo na čas zastoja tehničnega sredstva, bolezen zaposlenih …
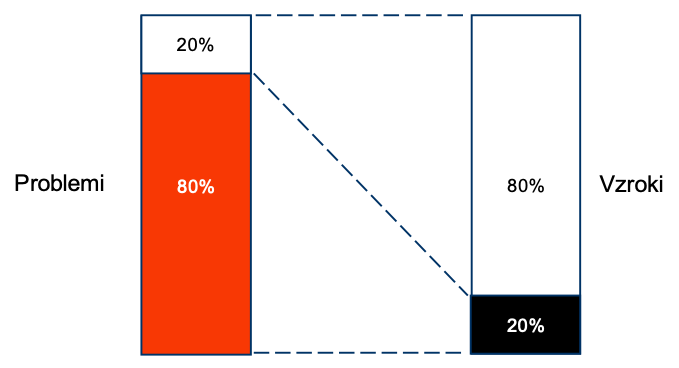
Primer 24:
Podjetje, ki proizvaja lesena okna, ugotavlja, da ima preveč izvržka. Odločili so se, da bodo stanje spremljali en mesec (20 delovnih dni), in sicer vsak dan. Vzroke za izvržek so razdelili v šest kategorij: napačna dimenzija, napačna barva, poškodba okvirja, zlomljeno steklo, nedelovanje mehanizma in slabo tesnjenje. Za spodnje podatke o številu napak po dnevih so izdelali kontrolni list (Slika 66) in Paretov diagram (Slika 67). Po opravljeni analizi so ugotovili, da podjetju povzročata največ težav napačna barva oken in poškodba okvirja (več kakor 70 % vsega izvržka, Slika 68). Največji učinek bodo torej dosegli, če se lotijo odpravljanja obeh vzrokov:
DAN | 1 | 2 | 3 | 4 | 5 | 6 | 7 | 8 | 9 | 10 | 11 | 12 | 13 | 14 | 15 | 16 | 17 | 18 | 19 | 20 |
---|---|---|---|---|---|---|---|---|---|---|---|---|---|---|---|---|---|---|---|---|
DIMENZIJA | 3 | 2 | 1 | 3 | 5 | 4 | 4 | 4 | 3 | 3 | 2 | 1 | 1 | 2 | 3 | 4 | 1 | 1 | 4 | 2 |
BARVA | 2 | 3 | 7 | 5 | 43 | 1 | 2 | 0 | 0 | 0 | 20 | 4 | 7 | 6 | 3 | 5 | 6 | 9 | 8 | 7 |
OKVIR | 2 | 3 | 5 | 6 | 0 | 7 | 6 | 4 | 3 | 3 | 0 | 4 | 5 | 0 | 5 | 2 | 2 | 1 | 1 | 2 |
STEKLO | 0 | 1 | 0 | 0 | 0 | 0 | 0 | 3 | 0 | 0 | 0 | 4 | 0 | 0 | 0 | 0 | 0 | 0 | 0 | 1 |
MEHANIZEM | 1 | 0 | 0 | 0 | 0 | 0 | 0 | 0 | 1 | 0 | 2 | 0 | 0 | 0 | 0 | 0 | 0 | 0 | 0 | 0 |
TESNENJE | 0 | 0 | 0 | 0 | 0 | 0 | 3 | 0 | 1 | 0 | 0 | 0 | 0 | 0 | 0 | 4 | 4 | 0 | 0 | 0 |
Slika 66. Kontrolni list napak po dnevih v podjetju za proizvodnjo lesenih oken
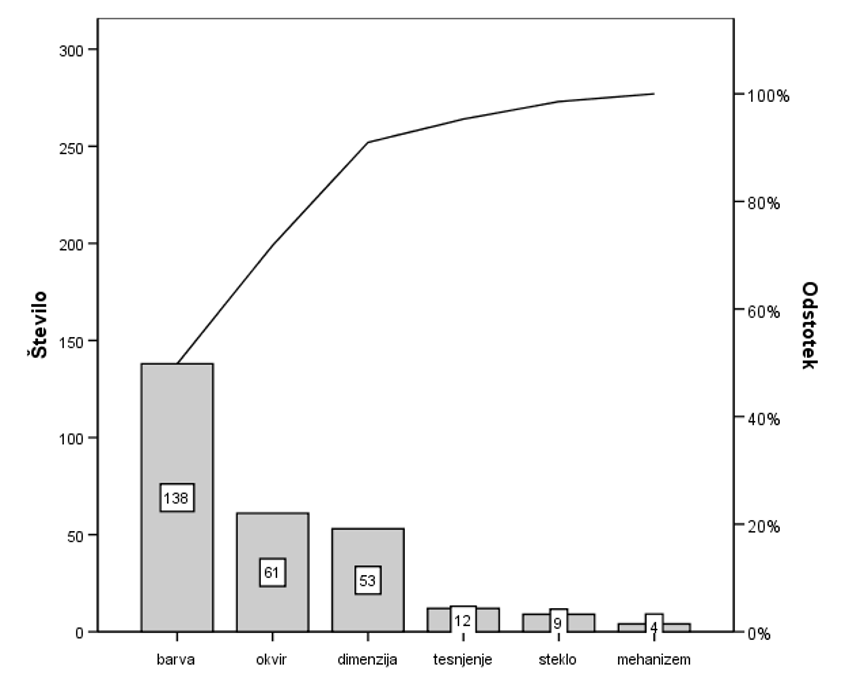
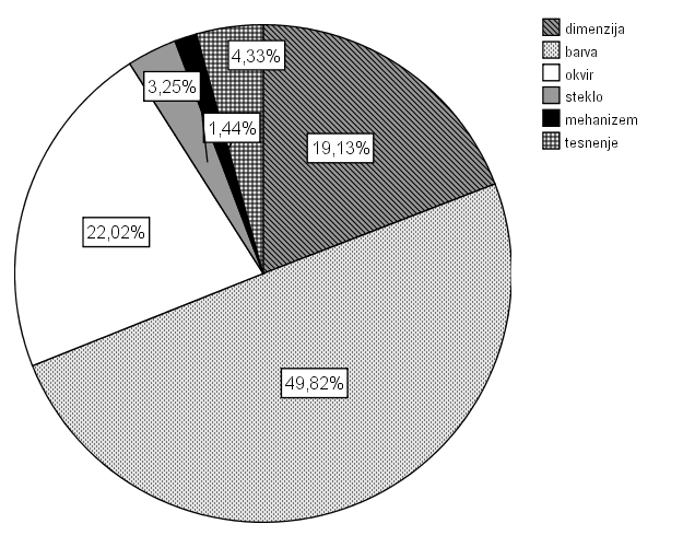